The medicinal use and method of administration dictate how pharmaceutical drugs are manufactured.
The product's packaging is meant to maintain the drug's potency and efficacy throughout its shelf life. An expiry date of 90 percent or more significant is the typical rule. The power and effectiveness of a medication can be affected by undesired impurities, and the pace of degradation can be accelerated.
This occurs when the original medicinal product is taken from its container and replaced with an ineffective or fake version. Unaware consumers are exposed to severe risks.
In pharmaceutical packaging, the issue is to ensure that the packaging has no harmful effects on the product and provides a flawless barrier. It is also essential for consumers to know whether the product is safe to ingest since the packaging should be tamper-proof.
Induction Cap Sealing Machine gives a solution by covering the whole mouth of the container with aluminium foil. This barrier effectively keeps contaminants out.
The seal provides even tamper evidence. Supply chains and routes from manufacturers occasionally cross-regional and national borders to consumers. When sealed with an induction cap, the package is durable and can endure transportation and storage.
For more than 18 years, R Technologies has worked with pharma firms to enhance packaging and provide more effective medications to customers.
The product's packaging is meant to maintain the drug's potency and efficacy throughout its shelf life. An expiry date of 90 percent or more significant is the typical rule. The power and effectiveness of a medication can be affected by undesired impurities, and the pace of degradation can be accelerated.
The products are at constant risk of exposure to contaminants during their entire supply chain journey.
- Vapor, moisture, gases, etc., can all create chemical pollution in the air. The product may alter in appearance due to water or vapor exposure. These are all signs that the product is unsuitable for human consumption and should be discarded.
- It is possible, however, for chemical changes to occur without any visible trace. Potency and effectiveness are reduced due to chemical breakdown. This leads certain medicines to generate toxic compounds, which in turn induce unpleasant reactions in patients.
- Bacteria, fungi, and molds are some of the organisms that can cause bio-contamination. Microorganisms are more likely to infect liquid and semi-solid formulations than solid formulations. If unintentionally ingested, microbial growth raises the chance of adverse consequences.
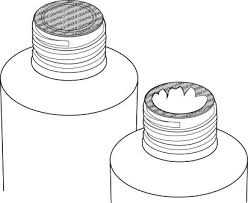
In pharmaceutical packaging, the issue is to ensure that the packaging has no harmful effects on the product and provides a flawless barrier. It is also essential for consumers to know whether the product is safe to ingest since the packaging should be tamper-proof.
Induction Cap Sealing Machine gives a solution by covering the whole mouth of the container with aluminium foil. This barrier effectively keeps contaminants out.
The seal provides even tamper evidence. Supply chains and routes from manufacturers occasionally cross-regional and national borders to consumers. When sealed with an induction cap, the package is durable and can endure transportation and storage.
For more than 18 years, R Technologies has worked with pharma firms to enhance packaging and provide more effective medications to customers.
Quality is our first concern whenever we acquire a product for personal use, such as drugs, drinks or cosmetics. There are several factors by which we evaluate quality. The safety of a product is another essential consideration.
Quality and safety are symbolised by a product delivered in a decent package with appropriate sealing, no leaks, and tamper evidence. Ingredients are guaranteed to be intact and shelf-stable with the help of the packaging. A product's packaging is a top priority for companies.
As well as being environmentally sustainable, user-friendly and not overly costly, packaging should conform to the object being packaged. When it comes to packing, induction sealing is a suitable option for all needs.
What is Induction Cap Sealing Machine?
The induction cap sealing method may be explained in a few sentences. Induction heating is used to seal the bottle mouth with the liner within the cap. As the bottle is passed beneath the cap sealing machine's head, the cap is sealed without touch.
The cap's lining is made up of many layers. To seal a container, a magnetic field must be created by passing the container beneath it. As the aluminium foil liner that seals the container's mouth is heated by the eddy current, the container's mouth is sealed.
With the cap closed, this non-invasive technique creates an airtight seal on the container. The contents are not affected by this process. Various plastic and glass containers are sealed using induction.
Knowing about the liner is crucial to understanding the induction sealing process. There are many layers of liner in the cap, each with a particular purpose. Pulpboard, wax, aluminium foil, and polymer are among the layers.
Soft and bonded to the cap, the pulp board is composed of a thin layer of paper. While being heated by induction, the wax melts and is absorbed into the pulp packing, releasing the foil. Polymer coating melts and closes foil on the mouth of the container with melting polymer coating.
Why should one select an induction cap sealing machine is the essential question? Customers and manufacturers should be aware of the advantages of this packing choice.
Cost-effective, leak-resistant, tamper-evident, assured quality, eco-friendly, higher productivity, and longer shelf life are just a few of the perks.
Quality and safety are symbolised by a product delivered in a decent package with appropriate sealing, no leaks, and tamper evidence. Ingredients are guaranteed to be intact and shelf-stable with the help of the packaging. A product's packaging is a top priority for companies.
As well as being environmentally sustainable, user-friendly and not overly costly, packaging should conform to the object being packaged. When it comes to packing, induction sealing is a suitable option for all needs.
What is Induction Cap Sealing Machine?
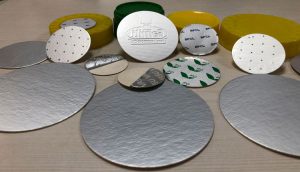
The cap's lining is made up of many layers. To seal a container, a magnetic field must be created by passing the container beneath it. As the aluminium foil liner that seals the container's mouth is heated by the eddy current, the container's mouth is sealed.
With the cap closed, this non-invasive technique creates an airtight seal on the container. The contents are not affected by this process. Various plastic and glass containers are sealed using induction.
What is Cap sealing Liner?
Knowing about the liner is crucial to understanding the induction sealing process. There are many layers of liner in the cap, each with a particular purpose. Pulpboard, wax, aluminium foil, and polymer are among the layers.
Soft and bonded to the cap, the pulp board is composed of a thin layer of paper. While being heated by induction, the wax melts and is absorbed into the pulp packing, releasing the foil. Polymer coating melts and closes foil on the mouth of the container with melting polymer coating.
Why Induction Cap Sealing?
Why should one select an induction cap sealing machine is the essential question? Customers and manufacturers should be aware of the advantages of this packing choice.
Cost-effective, leak-resistant, tamper-evident, assured quality, eco-friendly, higher productivity, and longer shelf life are just a few of the perks.
It's no secret that sealed packaging is essential when it comes to manufacturing and supply-related items. There are several reasons why this is the case. Businesses need to ensure that the things they offer have a tight-fitting cap. It makes them safe to eat.
When packaging items, an induction sealer is often used. Here, we'll take a closer look at the induction sealing method and its advantages.
How does the induction seal process work?
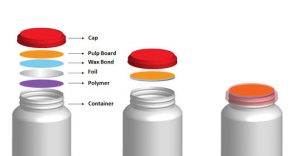
It is also known as cap sealing. Material-filled containers with foil-lined caps travel through an induction sealer. As containers travel through the sealer, energy from a regulated electromagnetic field is transferred to the containers.
As a result of this energy transfer, heat is generated on the aluminium foil liner. After then, the foil lining material melts due to the heat. Upon cooling, the liner forms an airtight seal around the container. In this way, the product is protected from contamination and leaking. Falsification and manipulation provide extra protection.
It is possible to seal nearly any type of product in the cosmetics, pharmaceutical, beauty care, and FMCG industries using an induction sealing machine Plastic or glass containers do not matter. All of them may be filled using the sealing machine.
The same technique may be used to seal liquids, cold foods, and dry goods. Lubricant oils, drinks, plants, powders, and much more are examples.
When choosing an induction liner, factors such as application and material must be taken into account. The liner is often made up of one or two pieces. The one-piece construction is laminated with foil. After the cap has been sealed, the liner is taken from it.
During two-piece construction, there is an additional pulpboard and wax layers. During the induction heating process, wax is melted and absorbed into the pulpboard. This layer of pulpboard allows for easier resealing after the foil liner has been removed from the bag.
R Technologies is a prominent provider of sealing systems for over four decades. We have a selection of induction sealing equipment that may meet your various demands. When it comes to boosting your business, there is no better place to go than here for trustworthy and cost-effective options. To receive a FREE quote on our machines, contact us now.
When packaging items, an induction sealer is often used. Here, we'll take a closer look at the induction sealing method and its advantages.
How does the induction seal process work?
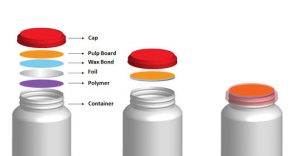
It is also known as cap sealing. Material-filled containers with foil-lined caps travel through an induction sealer. As containers travel through the sealer, energy from a regulated electromagnetic field is transferred to the containers.
As a result of this energy transfer, heat is generated on the aluminium foil liner. After then, the foil lining material melts due to the heat. Upon cooling, the liner forms an airtight seal around the container. In this way, the product is protected from contamination and leaking. Falsification and manipulation provide extra protection.
Benefits of induction sealing
The following are just a few of the benefits of this new technology:
- When a product is still fresh, it's safe to eat. As a result of the induction sealing process, the product is protected against contamination by external agents. Product durability and longevity are also improved.
- If products are not correctly sealed, they may leak or deteriorate during shipment. Because they are closed, they are leak-proof. A seal on items also helps buyers realize that the product has not been tampered with in any way.
- Product packaging is typically subject to strict regulations set by regulatory agencies. It is possible to obtain tamper-resistant seals using induction sealing.
- An induction seal gives consumers peace of mind by assuring them that the product fulfills quality specifications. It immediately contributes to client satisfaction and helps to enhance it over time.
- Induction sealers produce electromagnetic induction. The transmission's speed and frequency allow for rapid sealing, which leads to quicker manufacturing.
What products can an induction machine seal?
It is possible to seal nearly any type of product in the cosmetics, pharmaceutical, beauty care, and FMCG industries using an induction sealing machine Plastic or glass containers do not matter. All of them may be filled using the sealing machine.
The same technique may be used to seal liquids, cold foods, and dry goods. Lubricant oils, drinks, plants, powders, and much more are examples.
How to choose the right container and liner materials?
When choosing an induction liner, factors such as application and material must be taken into account. The liner is often made up of one or two pieces. The one-piece construction is laminated with foil. After the cap has been sealed, the liner is taken from it.
During two-piece construction, there is an additional pulpboard and wax layers. During the induction heating process, wax is melted and absorbed into the pulpboard. This layer of pulpboard allows for easier resealing after the foil liner has been removed from the bag.
Get your induction sealing machine today with R Technologies (Induction Cap Sealing Machine)
R Technologies is a prominent provider of sealing systems for over four decades. We have a selection of induction sealing equipment that may meet your various demands. When it comes to boosting your business, there is no better place to go than here for trustworthy and cost-effective options. To receive a FREE quote on our machines, contact us now.
The medicinal use and method of administration dictate how pharmaceutical drugs are manufactured.
The product's packaging is meant to maintain the drug's potency and efficacy throughout its shelf life. An expiry date of 90 percent or more significant is the typical rule. The power and effectiveness of a medication can be affected by undesired impurities, and the pace of degradation can be accelerated.
This occurs when the original medicinal product is taken from its container and replaced with an ineffective or fake version. Unaware consumers are exposed to severe risks.
In pharmaceutical packaging, the issue is to ensure that the packaging has no harmful effects on the product and provides a flawless barrier. It is also essential for consumers to know whether the product is safe to ingest since the packaging should be tamper-proof.
Induction Cap Sealing Machine gives a solution by covering the whole mouth of the container with aluminium foil. This barrier effectively keeps contaminants out.
The seal provides even tamper evidence. Supply chains and routes from manufacturers occasionally cross-regional and national borders to consumers. When sealed with an induction cap, the package is durable and can endure transportation and storage.
For more than 18 years, R Technologies has worked with pharma firms to enhance packaging and provide more effective medications to customers.
The product's packaging is meant to maintain the drug's potency and efficacy throughout its shelf life. An expiry date of 90 percent or more significant is the typical rule. The power and effectiveness of a medication can be affected by undesired impurities, and the pace of degradation can be accelerated.
The products are at constant risk of exposure to contaminants during their entire supply chain journey.
- Vapor, moisture, gases, etc., can all create chemical pollution in the air. The product may alter in appearance due to water or vapor exposure. These are all signs that the product is unsuitable for human consumption and should be discarded.
- It is possible, however, for chemical changes to occur without any visible trace. Potency and effectiveness are reduced due to chemical breakdown. This leads certain medicines to generate toxic compounds, which in turn induce unpleasant reactions in patients.
- Bacteria, fungi, and molds are some of the organisms that can cause bio-contamination. Microorganisms are more likely to infect liquid and semi-solid formulations than solid formulations. If unintentionally ingested, microbial growth raises the chance of adverse consequences.
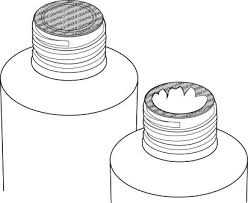
In pharmaceutical packaging, the issue is to ensure that the packaging has no harmful effects on the product and provides a flawless barrier. It is also essential for consumers to know whether the product is safe to ingest since the packaging should be tamper-proof.
Induction Cap Sealing Machine gives a solution by covering the whole mouth of the container with aluminium foil. This barrier effectively keeps contaminants out.
The seal provides even tamper evidence. Supply chains and routes from manufacturers occasionally cross-regional and national borders to consumers. When sealed with an induction cap, the package is durable and can endure transportation and storage.
For more than 18 years, R Technologies has worked with pharma firms to enhance packaging and provide more effective medications to customers.
Quality is our first concern whenever we acquire a product for personal use, such as drugs, drinks or cosmetics. There are several factors by which we evaluate quality. The safety of a product is another essential consideration.
Quality and safety are symbolised by a product delivered in a decent package with appropriate sealing, no leaks, and tamper evidence. Ingredients are guaranteed to be intact and shelf-stable with the help of the packaging. A product's packaging is a top priority for companies.
As well as being environmentally sustainable, user-friendly and not overly costly, packaging should conform to the object being packaged. When it comes to packing, induction sealing is a suitable option for all needs.
What is Induction Cap Sealing Machine?
The induction cap sealing method may be explained in a few sentences. Induction heating is used to seal the bottle mouth with the liner within the cap. As the bottle is passed beneath the cap sealing machine's head, the cap is sealed without touch.
The cap's lining is made up of many layers. To seal a container, a magnetic field must be created by passing the container beneath it. As the aluminium foil liner that seals the container's mouth is heated by the eddy current, the container's mouth is sealed.
With the cap closed, this non-invasive technique creates an airtight seal on the container. The contents are not affected by this process. Various plastic and glass containers are sealed using induction.
Knowing about the liner is crucial to understanding the induction sealing process. There are many layers of liner in the cap, each with a particular purpose. Pulpboard, wax, aluminium foil, and polymer are among the layers.
Soft and bonded to the cap, the pulp board is composed of a thin layer of paper. While being heated by induction, the wax melts and is absorbed into the pulp packing, releasing the foil. Polymer coating melts and closes foil on the mouth of the container with melting polymer coating.
Why should one select an induction cap sealing machine is the essential question? Customers and manufacturers should be aware of the advantages of this packing choice.
Cost-effective, leak-resistant, tamper-evident, assured quality, eco-friendly, higher productivity, and longer shelf life are just a few of the perks.
Quality and safety are symbolised by a product delivered in a decent package with appropriate sealing, no leaks, and tamper evidence. Ingredients are guaranteed to be intact and shelf-stable with the help of the packaging. A product's packaging is a top priority for companies.
As well as being environmentally sustainable, user-friendly and not overly costly, packaging should conform to the object being packaged. When it comes to packing, induction sealing is a suitable option for all needs.
What is Induction Cap Sealing Machine?
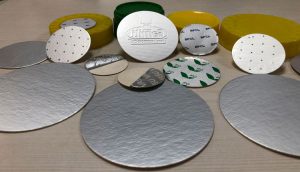
The cap's lining is made up of many layers. To seal a container, a magnetic field must be created by passing the container beneath it. As the aluminium foil liner that seals the container's mouth is heated by the eddy current, the container's mouth is sealed.
With the cap closed, this non-invasive technique creates an airtight seal on the container. The contents are not affected by this process. Various plastic and glass containers are sealed using induction.
What is Cap sealing Liner?
Knowing about the liner is crucial to understanding the induction sealing process. There are many layers of liner in the cap, each with a particular purpose. Pulpboard, wax, aluminium foil, and polymer are among the layers.
Soft and bonded to the cap, the pulp board is composed of a thin layer of paper. While being heated by induction, the wax melts and is absorbed into the pulp packing, releasing the foil. Polymer coating melts and closes foil on the mouth of the container with melting polymer coating.
Why Induction Cap Sealing?
Why should one select an induction cap sealing machine is the essential question? Customers and manufacturers should be aware of the advantages of this packing choice.
Cost-effective, leak-resistant, tamper-evident, assured quality, eco-friendly, higher productivity, and longer shelf life are just a few of the perks.
It's no secret that sealed packaging is essential when it comes to manufacturing and supply-related items. There are several reasons why this is the case. Businesses need to ensure that the things they offer have a tight-fitting cap. It makes them safe to eat.
When packaging items, an induction sealer is often used. Here, we'll take a closer look at the induction sealing method and its advantages.
How does the induction seal process work?
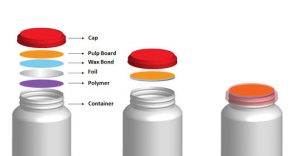
It is also known as cap sealing. Material-filled containers with foil-lined caps travel through an induction sealer. As containers travel through the sealer, energy from a regulated electromagnetic field is transferred to the containers.
As a result of this energy transfer, heat is generated on the aluminium foil liner. After then, the foil lining material melts due to the heat. Upon cooling, the liner forms an airtight seal around the container. In this way, the product is protected from contamination and leaking. Falsification and manipulation provide extra protection.
It is possible to seal nearly any type of product in the cosmetics, pharmaceutical, beauty care, and FMCG industries using an induction sealing machine Plastic or glass containers do not matter. All of them may be filled using the sealing machine.
The same technique may be used to seal liquids, cold foods, and dry goods. Lubricant oils, drinks, plants, powders, and much more are examples.
When choosing an induction liner, factors such as application and material must be taken into account. The liner is often made up of one or two pieces. The one-piece construction is laminated with foil. After the cap has been sealed, the liner is taken from it.
During two-piece construction, there is an additional pulpboard and wax layers. During the induction heating process, wax is melted and absorbed into the pulpboard. This layer of pulpboard allows for easier resealing after the foil liner has been removed from the bag.
R Technologies is a prominent provider of sealing systems for over four decades. We have a selection of induction sealing equipment that may meet your various demands. When it comes to boosting your business, there is no better place to go than here for trustworthy and cost-effective options. To receive a FREE quote on our machines, contact us now.
When packaging items, an induction sealer is often used. Here, we'll take a closer look at the induction sealing method and its advantages.
How does the induction seal process work?
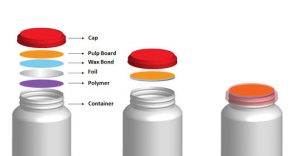
It is also known as cap sealing. Material-filled containers with foil-lined caps travel through an induction sealer. As containers travel through the sealer, energy from a regulated electromagnetic field is transferred to the containers.
As a result of this energy transfer, heat is generated on the aluminium foil liner. After then, the foil lining material melts due to the heat. Upon cooling, the liner forms an airtight seal around the container. In this way, the product is protected from contamination and leaking. Falsification and manipulation provide extra protection.
Benefits of induction sealing
The following are just a few of the benefits of this new technology:
- When a product is still fresh, it's safe to eat. As a result of the induction sealing process, the product is protected against contamination by external agents. Product durability and longevity are also improved.
- If products are not correctly sealed, they may leak or deteriorate during shipment. Because they are closed, they are leak-proof. A seal on items also helps buyers realize that the product has not been tampered with in any way.
- Product packaging is typically subject to strict regulations set by regulatory agencies. It is possible to obtain tamper-resistant seals using induction sealing.
- An induction seal gives consumers peace of mind by assuring them that the product fulfills quality specifications. It immediately contributes to client satisfaction and helps to enhance it over time.
- Induction sealers produce electromagnetic induction. The transmission's speed and frequency allow for rapid sealing, which leads to quicker manufacturing.
What products can an induction machine seal?
It is possible to seal nearly any type of product in the cosmetics, pharmaceutical, beauty care, and FMCG industries using an induction sealing machine Plastic or glass containers do not matter. All of them may be filled using the sealing machine.
The same technique may be used to seal liquids, cold foods, and dry goods. Lubricant oils, drinks, plants, powders, and much more are examples.
How to choose the right container and liner materials?
When choosing an induction liner, factors such as application and material must be taken into account. The liner is often made up of one or two pieces. The one-piece construction is laminated with foil. After the cap has been sealed, the liner is taken from it.
During two-piece construction, there is an additional pulpboard and wax layers. During the induction heating process, wax is melted and absorbed into the pulpboard. This layer of pulpboard allows for easier resealing after the foil liner has been removed from the bag.
Get your induction sealing machine today with R Technologies (Induction Cap Sealing Machine)
R Technologies is a prominent provider of sealing systems for over four decades. We have a selection of induction sealing equipment that may meet your various demands. When it comes to boosting your business, there is no better place to go than here for trustworthy and cost-effective options. To receive a FREE quote on our machines, contact us now.
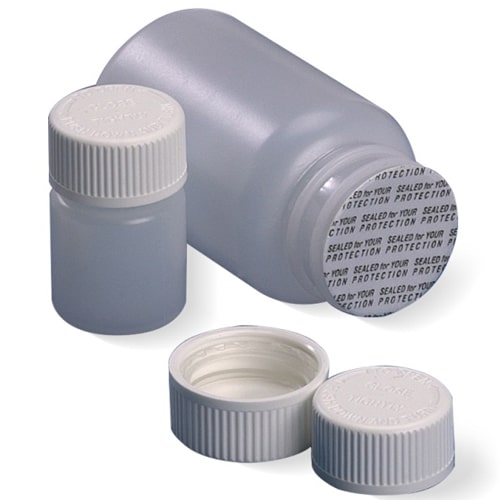
The medicinal use and method of administration dictate how pharmaceutical drugs are manufactured.
The product's packaging is meant to maintain the drug's potency and efficacy throughout its shelf life. An expiry date of 90 percent or more significant is the typical rule. The power and effectiveness of a medication can be affected by undesired impurities, and the pace of degradation can be accelerated.
This occurs when the original medicinal product is taken from its container and replaced with an ineffective or fake version. Unaware consumers are exposed to severe risks.
In pharmaceutical packaging, the issue is to ensure that the packaging has no harmful effects on the product and provides a flawless barrier. It is also essential for consumers to know whether the product is safe to ingest since the packaging should be tamper-proof.
Induction Cap Sealing Machine gives a solution by covering the whole mouth of the container with aluminium foil. This barrier effectively keeps contaminants out.
The seal provides even tamper evidence. Supply chains and routes from manufacturers occasionally cross-regional and national borders to consumers. When sealed with an induction cap, the package is durable and can endure transportation and storage.
For more than 18 years, R Technologies has worked with pharma firms to enhance packaging and provide more effective medications to customers.
The product's packaging is meant to maintain the drug's potency and efficacy throughout its shelf life. An expiry date of 90 percent or more significant is the typical rule. The power and effectiveness of a medication can be affected by undesired impurities, and the pace of degradation can be accelerated.
The products are at constant risk of exposure to contaminants during their entire supply chain journey.
- Vapor, moisture, gases, etc., can all create chemical pollution in the air. The product may alter in appearance due to water or vapor exposure. These are all signs that the product is unsuitable for human consumption and should be discarded.
- It is possible, however, for chemical changes to occur without any visible trace. Potency and effectiveness are reduced due to chemical breakdown. This leads certain medicines to generate toxic compounds, which in turn induce unpleasant reactions in patients.
- Bacteria, fungi, and molds are some of the organisms that can cause bio-contamination. Microorganisms are more likely to infect liquid and semi-solid formulations than solid formulations. If unintentionally ingested, microbial growth raises the chance of adverse consequences.
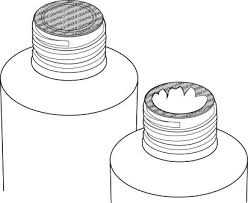
In pharmaceutical packaging, the issue is to ensure that the packaging has no harmful effects on the product and provides a flawless barrier. It is also essential for consumers to know whether the product is safe to ingest since the packaging should be tamper-proof.
Induction Cap Sealing Machine gives a solution by covering the whole mouth of the container with aluminium foil. This barrier effectively keeps contaminants out.
The seal provides even tamper evidence. Supply chains and routes from manufacturers occasionally cross-regional and national borders to consumers. When sealed with an induction cap, the package is durable and can endure transportation and storage.
For more than 18 years, R Technologies has worked with pharma firms to enhance packaging and provide more effective medications to customers.
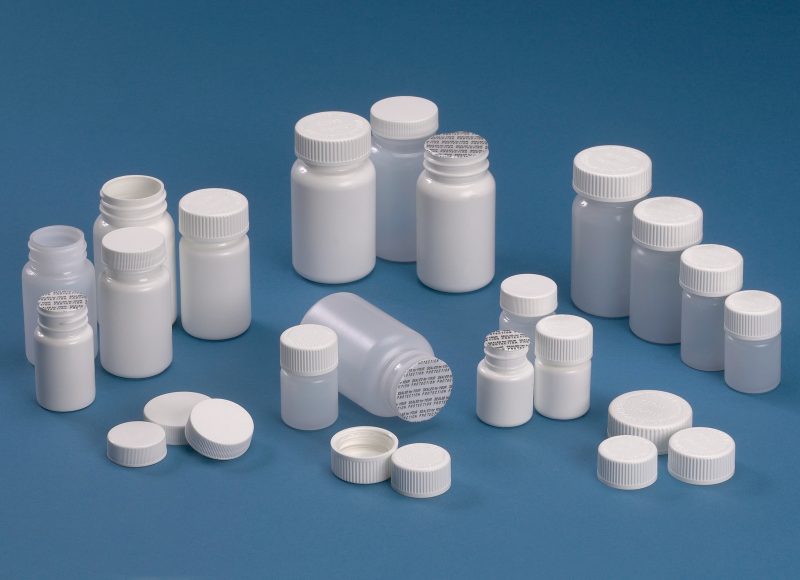
Quality is our first concern whenever we acquire a product for personal use, such as drugs, drinks or cosmetics. There are several factors by which we evaluate quality. The safety of a product is another essential consideration.
Quality and safety are symbolised by a product delivered in a decent package with appropriate sealing, no leaks, and tamper evidence. Ingredients are guaranteed to be intact and shelf-stable with the help of the packaging. A product's packaging is a top priority for companies.
As well as being environmentally sustainable, user-friendly and not overly costly, packaging should conform to the object being packaged. When it comes to packing, induction sealing is a suitable option for all needs.
What is Induction Cap Sealing Machine?
The induction cap sealing method may be explained in a few sentences. Induction heating is used to seal the bottle mouth with the liner within the cap. As the bottle is passed beneath the cap sealing machine's head, the cap is sealed without touch.
The cap's lining is made up of many layers. To seal a container, a magnetic field must be created by passing the container beneath it. As the aluminium foil liner that seals the container's mouth is heated by the eddy current, the container's mouth is sealed.
With the cap closed, this non-invasive technique creates an airtight seal on the container. The contents are not affected by this process. Various plastic and glass containers are sealed using induction.
Knowing about the liner is crucial to understanding the induction sealing process. There are many layers of liner in the cap, each with a particular purpose. Pulpboard, wax, aluminium foil, and polymer are among the layers.
Soft and bonded to the cap, the pulp board is composed of a thin layer of paper. While being heated by induction, the wax melts and is absorbed into the pulp packing, releasing the foil. Polymer coating melts and closes foil on the mouth of the container with melting polymer coating.
Why should one select an induction cap sealing machine is the essential question? Customers and manufacturers should be aware of the advantages of this packing choice.
Cost-effective, leak-resistant, tamper-evident, assured quality, eco-friendly, higher productivity, and longer shelf life are just a few of the perks.
Quality and safety are symbolised by a product delivered in a decent package with appropriate sealing, no leaks, and tamper evidence. Ingredients are guaranteed to be intact and shelf-stable with the help of the packaging. A product's packaging is a top priority for companies.
As well as being environmentally sustainable, user-friendly and not overly costly, packaging should conform to the object being packaged. When it comes to packing, induction sealing is a suitable option for all needs.
What is Induction Cap Sealing Machine?
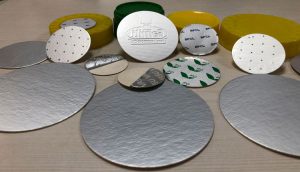
The cap's lining is made up of many layers. To seal a container, a magnetic field must be created by passing the container beneath it. As the aluminium foil liner that seals the container's mouth is heated by the eddy current, the container's mouth is sealed.
With the cap closed, this non-invasive technique creates an airtight seal on the container. The contents are not affected by this process. Various plastic and glass containers are sealed using induction.
What is Cap sealing Liner?
Knowing about the liner is crucial to understanding the induction sealing process. There are many layers of liner in the cap, each with a particular purpose. Pulpboard, wax, aluminium foil, and polymer are among the layers.
Soft and bonded to the cap, the pulp board is composed of a thin layer of paper. While being heated by induction, the wax melts and is absorbed into the pulp packing, releasing the foil. Polymer coating melts and closes foil on the mouth of the container with melting polymer coating.
Why Induction Cap Sealing?
Why should one select an induction cap sealing machine is the essential question? Customers and manufacturers should be aware of the advantages of this packing choice.
Cost-effective, leak-resistant, tamper-evident, assured quality, eco-friendly, higher productivity, and longer shelf life are just a few of the perks.
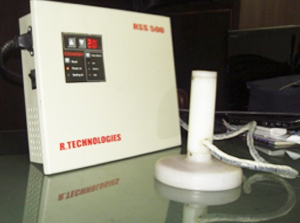
It's no secret that sealed packaging is essential when it comes to manufacturing and supply-related items. There are several reasons why this is the case. Businesses need to ensure that the things they offer have a tight-fitting cap. It makes them safe to eat.
When packaging items, an induction sealer is often used. Here, we'll take a closer look at the induction sealing method and its advantages.
How does the induction seal process work?
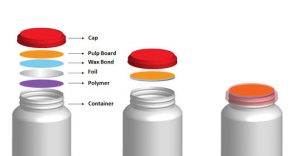
It is also known as cap sealing. Material-filled containers with foil-lined caps travel through an induction sealer. As containers travel through the sealer, energy from a regulated electromagnetic field is transferred to the containers.
As a result of this energy transfer, heat is generated on the aluminium foil liner. After then, the foil lining material melts due to the heat. Upon cooling, the liner forms an airtight seal around the container. In this way, the product is protected from contamination and leaking. Falsification and manipulation provide extra protection.
It is possible to seal nearly any type of product in the cosmetics, pharmaceutical, beauty care, and FMCG industries using an induction sealing machine Plastic or glass containers do not matter. All of them may be filled using the sealing machine.
The same technique may be used to seal liquids, cold foods, and dry goods. Lubricant oils, drinks, plants, powders, and much more are examples.
When choosing an induction liner, factors such as application and material must be taken into account. The liner is often made up of one or two pieces. The one-piece construction is laminated with foil. After the cap has been sealed, the liner is taken from it.
During two-piece construction, there is an additional pulpboard and wax layers. During the induction heating process, wax is melted and absorbed into the pulpboard. This layer of pulpboard allows for easier resealing after the foil liner has been removed from the bag.
R Technologies is a prominent provider of sealing systems for over four decades. We have a selection of induction sealing equipment that may meet your various demands. When it comes to boosting your business, there is no better place to go than here for trustworthy and cost-effective options. To receive a FREE quote on our machines, contact us now.
When packaging items, an induction sealer is often used. Here, we'll take a closer look at the induction sealing method and its advantages.
How does the induction seal process work?
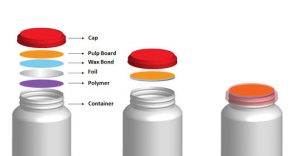
It is also known as cap sealing. Material-filled containers with foil-lined caps travel through an induction sealer. As containers travel through the sealer, energy from a regulated electromagnetic field is transferred to the containers.
As a result of this energy transfer, heat is generated on the aluminium foil liner. After then, the foil lining material melts due to the heat. Upon cooling, the liner forms an airtight seal around the container. In this way, the product is protected from contamination and leaking. Falsification and manipulation provide extra protection.
Benefits of induction sealing
The following are just a few of the benefits of this new technology:
- When a product is still fresh, it's safe to eat. As a result of the induction sealing process, the product is protected against contamination by external agents. Product durability and longevity are also improved.
- If products are not correctly sealed, they may leak or deteriorate during shipment. Because they are closed, they are leak-proof. A seal on items also helps buyers realize that the product has not been tampered with in any way.
- Product packaging is typically subject to strict regulations set by regulatory agencies. It is possible to obtain tamper-resistant seals using induction sealing.
- An induction seal gives consumers peace of mind by assuring them that the product fulfills quality specifications. It immediately contributes to client satisfaction and helps to enhance it over time.
- Induction sealers produce electromagnetic induction. The transmission's speed and frequency allow for rapid sealing, which leads to quicker manufacturing.
What products can an induction machine seal?
It is possible to seal nearly any type of product in the cosmetics, pharmaceutical, beauty care, and FMCG industries using an induction sealing machine Plastic or glass containers do not matter. All of them may be filled using the sealing machine.
The same technique may be used to seal liquids, cold foods, and dry goods. Lubricant oils, drinks, plants, powders, and much more are examples.
How to choose the right container and liner materials?
When choosing an induction liner, factors such as application and material must be taken into account. The liner is often made up of one or two pieces. The one-piece construction is laminated with foil. After the cap has been sealed, the liner is taken from it.
During two-piece construction, there is an additional pulpboard and wax layers. During the induction heating process, wax is melted and absorbed into the pulpboard. This layer of pulpboard allows for easier resealing after the foil liner has been removed from the bag.
Get your induction sealing machine today with R Technologies (Induction Cap Sealing Machine)
R Technologies is a prominent provider of sealing systems for over four decades. We have a selection of induction sealing equipment that may meet your various demands. When it comes to boosting your business, there is no better place to go than here for trustworthy and cost-effective options. To receive a FREE quote on our machines, contact us now.
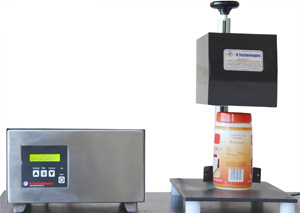
for medication, such seals can "not be worked out and reappeared without any visible damage" required by medicines the Food and Drug Administration).
The seals are provided within the caps and constructed of an aluminium foil layer, typically sandwiched between other materials. The aluminium layer with wax, paper and adhesive layers is usually held at the top of your hat. Below is a polymer film layer that sticks the metal to the bottle opening.
Once sealed, the bottles are placed under an induction coil, heating the aluminium foil. This heat releases the foil off the cap simultaneously and screws it into the container. A hand-held device or a higher speed conveyor belt can be used to pass the bottle beneath an induction coil. Many systems are waterless today (air-cooled), taking up approximately half the size of previous water-cooled systems.
While it is common and familiar to combine multiple individual products with shrinking wrapping, induction sealing is still a preferable choice in many circumstances. Some benefits include:
Less Packaging: Shrink-wrap should cover the container entirely without overlapping flaps to comply with the FDA standards. Induction sealing, by comparison, requires only sufficient material to cover the hole.
The heat to form the seal is less required.
A better, safer seal than the shrink-wrap screws that cover just the container's lid and neck.
The faster sealing procedure, especially for conveyor belt applications.
Less machine space is needed. Only three to five metres of the conveyor belt can provide a whole system demand space.
First, calculate how many containers you need to seal, as well as their size and forms. Look for a system that can adapt to changes in packing. See much better if your company can develop up. This figure indicates that most vendors can fit caps from 15 to120 mm, up to 180 feet of conveyor per minute.
Next, decide what power you're going to require. Depending on the number of containers you must seal each minute, the inductive dumpers might demand from 0.5kw to 6kw.
Before you purchase:
Let R Technologies Help You.
Call or check our website here at +91 22 27688599 to discuss our capping options and how they are suitable for your system of induction sealing. You may find here more suggestions on selecting an induction cap sealing system. me to discover your optimal operating window once your induction sealing system is set up. In addition to visually damaging your container, too much heat can also cause the seal to break for days.
The seals are provided within the caps and constructed of an aluminium foil layer, typically sandwiched between other materials. The aluminium layer with wax, paper and adhesive layers is usually held at the top of your hat. Below is a polymer film layer that sticks the metal to the bottle opening.
Once sealed, the bottles are placed under an induction coil, heating the aluminium foil. This heat releases the foil off the cap simultaneously and screws it into the container. A hand-held device or a higher speed conveyor belt can be used to pass the bottle beneath an induction coil. Many systems are waterless today (air-cooled), taking up approximately half the size of previous water-cooled systems.
Induction Sealing vs Shrink Wrapping
While it is common and familiar to combine multiple individual products with shrinking wrapping, induction sealing is still a preferable choice in many circumstances. Some benefits include:
Less Packaging: Shrink-wrap should cover the container entirely without overlapping flaps to comply with the FDA standards. Induction sealing, by comparison, requires only sufficient material to cover the hole.
The heat to form the seal is less required.
A better, safer seal than the shrink-wrap screws that cover just the container's lid and neck.
The faster sealing procedure, especially for conveyor belt applications.
Less machine space is needed. Only three to five metres of the conveyor belt can provide a whole system demand space.
How to Get Started
First, calculate how many containers you need to seal, as well as their size and forms. Look for a system that can adapt to changes in packing. See much better if your company can develop up. This figure indicates that most vendors can fit caps from 15 to120 mm, up to 180 feet of conveyor per minute.
Next, decide what power you're going to require. Depending on the number of containers you must seal each minute, the inductive dumpers might demand from 0.5kw to 6kw.
Before you purchase:
- Discuss with your supplier and let them know all your product specifics and packaging.
- Ask whether they assist you with your phone problems or whether you constantly have to wait for a service person.
- See whether their power supply is separate from their sealing systems, so if only one piece has to be changed, you don't have to return the complete machine.
Let R Technologies Help You.
Call or check our website here at +91 22 27688599 to discuss our capping options and how they are suitable for your system of induction sealing. You may find here more suggestions on selecting an induction cap sealing system. me to discover your optimal operating window once your induction sealing system is set up. In addition to visually damaging your container, too much heat can also cause the seal to break for days.
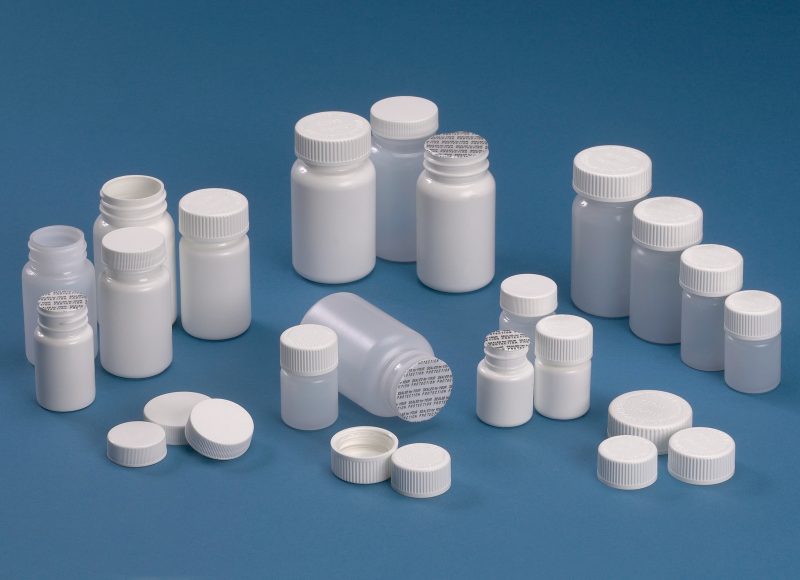
This is the age of product, commercial and banding variations. In this, the packaging is of the utmost importance. In recent years there has been a growing awareness and demand for packaging.
R Technologies includes filling, capping, sealing and labelling with associated facilities for the filling of bottles. Bottle packaging verities are a vital instrument to package, utilise, preserve, protect, transport, and distribute goods in any industry. It also adds the possibility to sort, differentiate, batch, code, and many other things.
The package is not restricted to certain businesses; R Technologies includes diverse sectors such as Pharmaceutics, Ayurvedic, Cosmetics, Personal Care, Home Care, Cleaning Products, Food & Beverage, Dairy, Saxony, Ghee, Edible Oil. R Technologies offers different types of Filling, Sealing and Labelling technology to deliver high-end products at affordable prices. We integrate both conventional designs and completely tailored, practical and successful solutions with top-quality cost efficiency.
Based on the above, R Technologies provides the continuous full-automation induction cap sealing system with digital keyboard controls, PLC HMI touchscreens with a variety of types of pump filling technologies such as volumetric, piston, gravimetric, weigher, load-based & sealing, inductivity & drive technology, roller, pneumatic cylinder based, timer-based technology pick & place.
Pneumatic stoppers, fibreglass holders, actuators, jacket tanks and hoppers, stirrers, timers, tapering, guide boxes, supports and many more are supplied with a range of technology to suit the requirements of the package. R Technologies is suitable for all industries and product variations. We understand the client requirements and apply our ability to develop the right machine.
R Technologies includes filling, capping, sealing and labelling with associated facilities for the filling of bottles. Bottle packaging verities are a vital instrument to package, utilise, preserve, protect, transport, and distribute goods in any industry. It also adds the possibility to sort, differentiate, batch, code, and many other things.
The package is not restricted to certain businesses; R Technologies includes diverse sectors such as Pharmaceutics, Ayurvedic, Cosmetics, Personal Care, Home Care, Cleaning Products, Food & Beverage, Dairy, Saxony, Ghee, Edible Oil. R Technologies offers different types of Filling, Sealing and Labelling technology to deliver high-end products at affordable prices. We integrate both conventional designs and completely tailored, practical and successful solutions with top-quality cost efficiency.
Based on the above, R Technologies provides the continuous full-automation induction cap sealing system with digital keyboard controls, PLC HMI touchscreens with a variety of types of pump filling technologies such as volumetric, piston, gravimetric, weigher, load-based & sealing, inductivity & drive technology, roller, pneumatic cylinder based, timer-based technology pick & place.
Pneumatic stoppers, fibreglass holders, actuators, jacket tanks and hoppers, stirrers, timers, tapering, guide boxes, supports and many more are supplied with a range of technology to suit the requirements of the package. R Technologies is suitable for all industries and product variations. We understand the client requirements and apply our ability to develop the right machine.
for medication, such seals can "not be worked out and reappeared without any visible damage" required by medicines the Food and Drug Administration).
The seals are provided within the caps and constructed of an aluminium foil layer, typically sandwiched between other materials. The aluminium layer with wax, paper and adhesive layers is usually held at the top of your hat. Below is a polymer film layer that sticks the metal to the bottle opening.
Once sealed, the bottles are placed under an induction coil, heating the aluminium foil. This heat releases the foil off the cap simultaneously and screws it into the container. A hand-held device or a higher speed conveyor belt can be used to pass the bottle beneath an induction coil. Many systems are waterless today (air-cooled), taking up approximately half the size of previous water-cooled systems.
While it is common and familiar to combine multiple individual products with shrinking wrapping, induction sealing is still a preferable choice in many circumstances. Some benefits include:
Less Packaging: Shrink-wrap should cover the container entirely without overlapping flaps to comply with the FDA standards. Induction sealing, by comparison, requires only sufficient material to cover the hole.
The heat to form the seal is less required.
A better, safer seal than the shrink-wrap screws that cover just the container's lid and neck.
The faster sealing procedure, especially for conveyor belt applications.
Less machine space is needed. Only three to five metres of the conveyor belt can provide a whole system demand space.
First, calculate how many containers you need to seal, as well as their size and forms. Look for a system that can adapt to changes in packing. See much better if your company can develop up. This figure indicates that most vendors can fit caps from 15 to120 mm, up to 180 feet of conveyor per minute.
Next, decide what power you're going to require. Depending on the number of containers you must seal each minute, the inductive dumpers might demand from 0.5kw to 6kw.
Before you purchase:
Let R Technologies Help You.
Call or check our website here at +91 22 27688599 to discuss our capping options and how they are suitable for your system of induction sealing. You may find here more suggestions on selecting an induction cap sealing system. me to discover your optimal operating window once your induction sealing system is set up. In addition to visually damaging your container, too much heat can also cause the seal to break for days.
The seals are provided within the caps and constructed of an aluminium foil layer, typically sandwiched between other materials. The aluminium layer with wax, paper and adhesive layers is usually held at the top of your hat. Below is a polymer film layer that sticks the metal to the bottle opening.
Once sealed, the bottles are placed under an induction coil, heating the aluminium foil. This heat releases the foil off the cap simultaneously and screws it into the container. A hand-held device or a higher speed conveyor belt can be used to pass the bottle beneath an induction coil. Many systems are waterless today (air-cooled), taking up approximately half the size of previous water-cooled systems.
Induction Sealing vs Shrink Wrapping
While it is common and familiar to combine multiple individual products with shrinking wrapping, induction sealing is still a preferable choice in many circumstances. Some benefits include:
Less Packaging: Shrink-wrap should cover the container entirely without overlapping flaps to comply with the FDA standards. Induction sealing, by comparison, requires only sufficient material to cover the hole.
The heat to form the seal is less required.
A better, safer seal than the shrink-wrap screws that cover just the container's lid and neck.
The faster sealing procedure, especially for conveyor belt applications.
Less machine space is needed. Only three to five metres of the conveyor belt can provide a whole system demand space.
How to Get Started
First, calculate how many containers you need to seal, as well as their size and forms. Look for a system that can adapt to changes in packing. See much better if your company can develop up. This figure indicates that most vendors can fit caps from 15 to120 mm, up to 180 feet of conveyor per minute.
Next, decide what power you're going to require. Depending on the number of containers you must seal each minute, the inductive dumpers might demand from 0.5kw to 6kw.
Before you purchase:
- Discuss with your supplier and let them know all your product specifics and packaging.
- Ask whether they assist you with your phone problems or whether you constantly have to wait for a service person.
- See whether their power supply is separate from their sealing systems, so if only one piece has to be changed, you don't have to return the complete machine.
Let R Technologies Help You.
Call or check our website here at +91 22 27688599 to discuss our capping options and how they are suitable for your system of induction sealing. You may find here more suggestions on selecting an induction cap sealing system. me to discover your optimal operating window once your induction sealing system is set up. In addition to visually damaging your container, too much heat can also cause the seal to break for days.
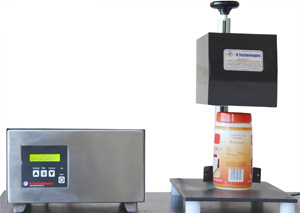
This is the age of product, commercial and banding variations. In this, the packaging is of the utmost importance. In recent years there has been a growing awareness and demand for packaging.
R Technologies includes filling, capping, sealing and labelling with associated facilities for the filling of bottles. Bottle packaging verities are a vital instrument to package, utilise, preserve, protect, transport, and distribute goods in any industry. It also adds the possibility to sort, differentiate, batch, code, and many other things.
The package is not restricted to certain businesses; R Technologies includes diverse sectors such as Pharmaceutics, Ayurvedic, Cosmetics, Personal Care, Home Care, Cleaning Products, Food & Beverage, Dairy, Saxony, Ghee, Edible Oil. R Technologies offers different types of Filling, Sealing and Labelling technology to deliver high-end products at affordable prices. We integrate both conventional designs and completely tailored, practical and successful solutions with top-quality cost efficiency.
Based on the above, R Technologies provides the continuous full-automation induction cap sealing system with digital keyboard controls, PLC HMI touchscreens with a variety of types of pump filling technologies such as volumetric, piston, gravimetric, weigher, load-based & sealing, inductivity & drive technology, roller, pneumatic cylinder based, timer-based technology pick & place.
Pneumatic stoppers, fibreglass holders, actuators, jacket tanks and hoppers, stirrers, timers, tapering, guide boxes, supports and many more are supplied with a range of technology to suit the requirements of the package. R Technologies is suitable for all industries and product variations. We understand the client requirements and apply our ability to develop the right machine.
R Technologies includes filling, capping, sealing and labelling with associated facilities for the filling of bottles. Bottle packaging verities are a vital instrument to package, utilise, preserve, protect, transport, and distribute goods in any industry. It also adds the possibility to sort, differentiate, batch, code, and many other things.
The package is not restricted to certain businesses; R Technologies includes diverse sectors such as Pharmaceutics, Ayurvedic, Cosmetics, Personal Care, Home Care, Cleaning Products, Food & Beverage, Dairy, Saxony, Ghee, Edible Oil. R Technologies offers different types of Filling, Sealing and Labelling technology to deliver high-end products at affordable prices. We integrate both conventional designs and completely tailored, practical and successful solutions with top-quality cost efficiency.
Based on the above, R Technologies provides the continuous full-automation induction cap sealing system with digital keyboard controls, PLC HMI touchscreens with a variety of types of pump filling technologies such as volumetric, piston, gravimetric, weigher, load-based & sealing, inductivity & drive technology, roller, pneumatic cylinder based, timer-based technology pick & place.
Pneumatic stoppers, fibreglass holders, actuators, jacket tanks and hoppers, stirrers, timers, tapering, guide boxes, supports and many more are supplied with a range of technology to suit the requirements of the package. R Technologies is suitable for all industries and product variations. We understand the client requirements and apply our ability to develop the right machine.
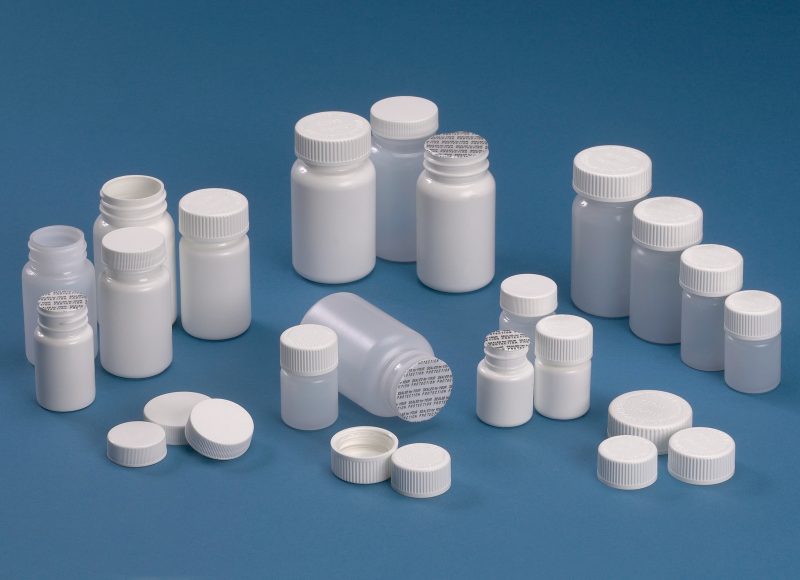